W ostatnim czasie niemiecka Grupa Turck zdecydowała o otwarciu pierwszego zakładu produkcyjnego w Europie Środkowo-Wschodniej. Pomimo dużej konkurencji niemiecki lider automatyki przemysłowej zdecydował się na zlokalizowanie zakładu w Lublinie, odrzucając ofertę Litwy, Węgier czy Rumunii. O procesie otwarcia nowego zakładu, specjalizacji, a także budowaniu nowego zespołu w Lublinie porozmawialiśmy z Przemysławem Brzeziewskim – dyrektorem zarządzającym Turck Automation Technology w Lublinie.
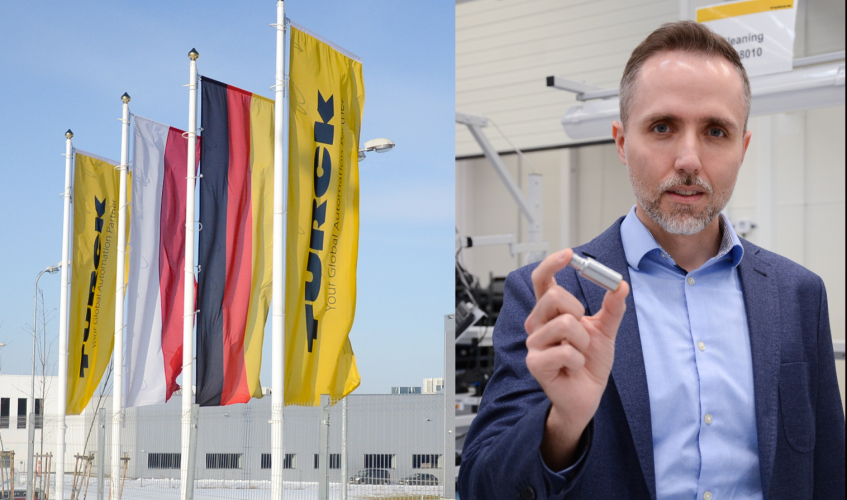
Naszą rozmowę chciałbym rozpocząć od najważniejszych informacji na temat firmy.
Turck jest globalną grupą kapitałową, która dziś posiada 7 zakładów na całym świecie. Dużą część działalności prowadzi w Europie i Stanach Zjednoczonych Ameryki. Zatrudnia dziś około 5 tys. pracowników.
Firma zajmuje się przede wszystkim produkcją elementów automatyki przemysłowej. Swoim klientom proponujemy rozwiązania takie jak czujniki, systemy sieciowe I/O, produkty połączeniowe, interfejsy HMI oraz systemy RFID. Naszą specjalizacją jest łączność i sterowanie elementami automatyki.
Turck to firma z długoletnią historią, w której zostały zakorzenione tradycje…
Rzeczywiście tak jest. Myślę, że jest to też dobry wstęp do naszej rozmowy, ponieważ nasza kultura pracy jest mocno związana z historią firmy. Aby dobrze przedstawić cały kontekst musimy cofnąć się w czasie do lat 60. XX wieku kiedy dwaj bracia (Hans i Werner Turck) zdecydowali, że założą firmę. Z perspektywy czasu ich współpraca była bardzo udana, ponieważ jeden z nich specjalizował się w sprawach inżynieryjnych (czyli projektowaniem i wytwarzaniem produktów). Drugi, zajmował się marketingiem, dystrybucją i sprzedażą. Bracia zarządzali firmą przez prawie 45 lat. Niestety obydwaj zmarli w 2015 roku…
To ważne, aby o tym powiedzieć, ponieważ wielu pracowników pamięta jeszcze właścicieli. To były bardzo charyzmatyczne osoby, które bardzo dużo znaczyły dla całej lokalnej społeczności. Odcisnęli piętno na atmosferze, czy tak jak wspomniałem na początku naszej rozmowy – kulturze pracy. Kiedy ich zabrakło, nastąpiła bardzo duża zmiana… Firma pomimo swojego rozmiaru i międzynarodowego charakteru zachowała swój rodzinny i zdroworozsądkowy charakter.
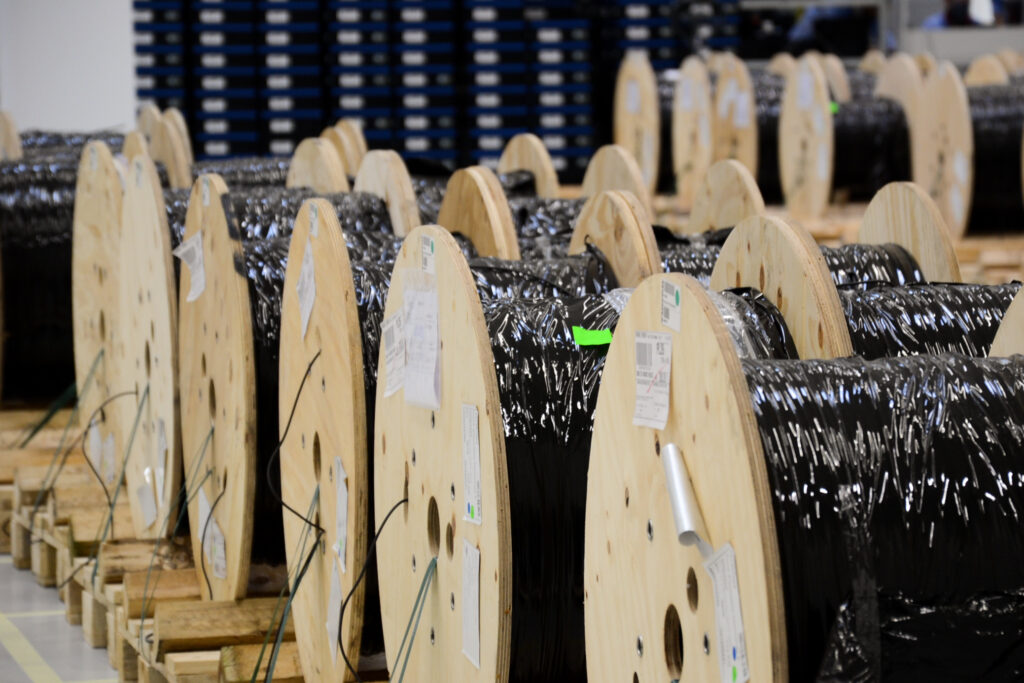
Tradycja i historia na pewno są bardzo ważne. Mimo to dzisiejsze czasy znacząco różnią się od tamtych. Upraszczając można powiedzieć, że charakteryzuje je duży postęp technologiczny, który poniekąd dyktujecie swoimi produktami. Czy możemy już mówić o erze przemysłu 4.0 w Polsce?
My, jako firma Turck, z jednej strony jesteśmy dostawcą technologii (ponieważ dostarczamy elementy, które składają się na wdrożenie w obszaru przemysłu 4.0), a z drugiej strony sami jesteśmy jej użytkownikami. Prowadzimy zakłady produkcyjne, które muszą spełniać wszelkie współczesne normy i zapewniać konkurencyjną efektywność. To wszystko składa się na to, że temat przemysłu 4.0 jest dla nas bardzo istotny.
Ale zacznijmy od początku. Przemysł 4.0 to istotny przełom w historii przemysłu czy gospodarki. Określenie go ewolucją to za mało, ponieważ zakłada on nie tyle wynajdowanie nowych rozwiązań co łączenie technologii, które są z nami już od jakiegoś czasu. Powszechnie definiuje się to pojęcie jako wdrożenia oparte na takich technologiach jak np. roboty przemysłowe, internet rzeczy, big data, rozwiązania chmurowe, druk 3D, rozszerzona rzeczywistość, cyberbezpieczeństwo i wiele, wiele innych. Można tak wymieniać jeszcze długo.
Odpowiadając na pytanie dotyczące Polski, czy w ogóle gospodarki, uważam że jesteśmy dopiero na początku tej drogi. Dziś bardzo często naszym ograniczeniem nie są możliwości technologii, a nasza wyobraźnia i pomysły na innowacyjne zastosowania w przemyśle. Kluczem do sukcesu będą osoby mające otwartą głowę, kreatywność i odwagę we wdrażaniu nowych rozwiązań. Jestem przekonany, że takich osób w Polsce nie brakuje…
Jakie inteligentne rozwiązania TURCK wprowadza do przemysłu?
Naszymi klientami są przede wszystkim producenci maszyn, urządzeń i pojazdów. My jako firma specjalizujemy się w różnego rodzaju czujnikach. Jak dobrze wiemy, dziś prawie każde urządzenie jest wyposażone w tego typu rozwiązania. Za przykład mogę podać zwykły samochód osobowy, gdzie mamy przecież czujniki sprawdzające zamknięcie drzwi, poziomy płynów, zapięcie pasów, czujniki parkowania, czy te, które sprawdzają ciśnienie w oponach. Takich rozwiązań możemy mnożyć bez końca. Każde nowe urządzenie jest dzisiaj coraz bardziej „inteligentne”, to znaczy monitoruje i analizuje na bieżąco parametry swojej pracy i swojego otoczenia. Nasze rozwiązania tworzą fundamenty takiej „inteligencji”.
Jednym z wielu rozwiązań, proponowanych przez naszą firmę, jest monitoring wibracji maszyny. Zamontowanie takiego urządzenia ma wiele zalet. Pozwala między innymi wcześniej przewidzieć nadchodzącą awarię lub nieprawidłową pracę maszyny. Ponadto przypomina o szybszej wymianie części, które mogą znacząco wpłynąć na jakość wykonywanej pracy.
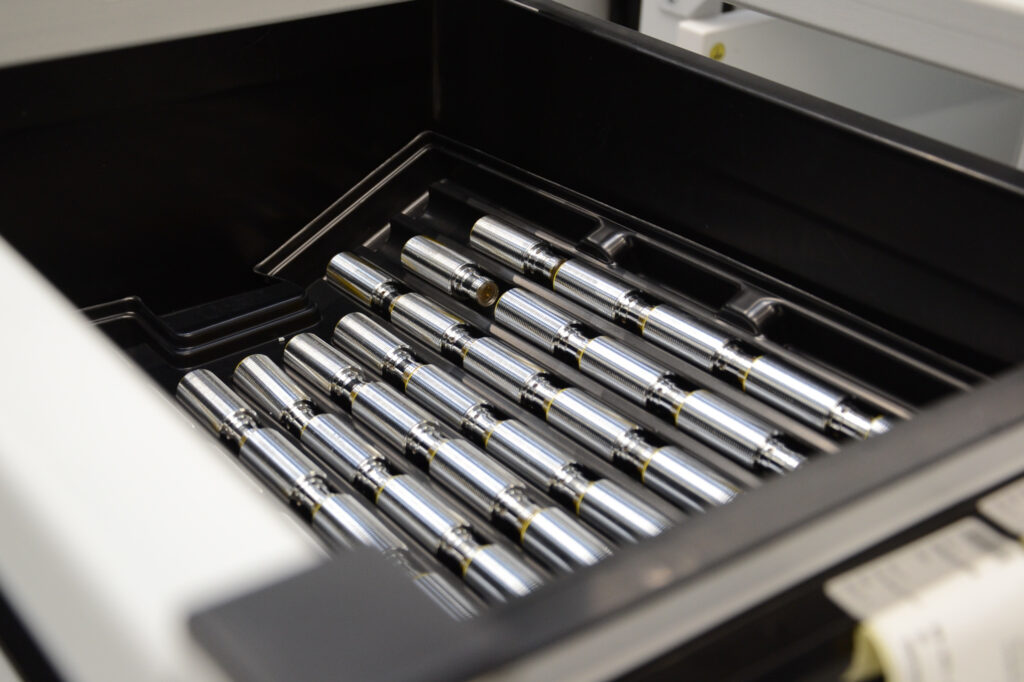
Nowo otwarta fabryka w Lublinie jest jedną z najnowocześniejszych w państwa firmie. Co wyróżnia ją na tle pozostałych oddziałów?
My, podobnie jak wiele innych firm działających w obszarze automatyki przemysłowej, mamy produkcję o charakterze High Mix – Low Volume. Oznacza to, że produkujemy bardzo dużo modeli naszych wyrobów w stosunkowo krótkich i niedużych seriach. Nie jest to typ produkcji pozwalający na wysoki poziom automatyzacji, dlatego nasze wdrożenie z obszaru przemysłu 4.0 koncentrujemy przede wszystkim na systemach informatycznych i zarządzaniu przepływem informacji w procesie produkcyjnym.
Dobrym przykładem jest wdrażany przez nas system ERP. Praca operatora jest wspierana przez system na każdym stanowisku pracy. Umożliwia to zarządzanie produkcją zgodnie z filozofią „paperless manufacturing”, czyli bez konieczności używania jakichkolwiek dokumentów papierowych. Dzięki temu każdy pracownik może uzyskać informacje na temat realizowanego zlecenia, a także rejestrować czynności, które sam wykonał. To znacząco ułatwia i przyspiesza proces. Zależy nam na integracji maszyn i urządzeń, aby były one w jak największym stopniu obsługiwane bezpośrednio przez system informatyczny.
To co nas wyróżnia to bardzo duża elastyczność i możliwość szybkiego reagowania na zapotrzebowanie zgłaszane przez klientów. W zakładzie w Lublinie nie planujemy magazynu wyrobów gotowych, który znajduje się w nowoczesnym centrum dystrybucji w Niemczech.
A jakie urządzenia produkowane są na liniach w Lublinie?
Produkujemy różnego typu czujniki indukcyjne, a w lutym uruchamiamy nową linię produkcyjną, na której rozpoczniemy produkcję szerokiego zakresu konfekcjonowanych kabli połączeniowych ze złączami M8 i M12.
Na czym polega największa trudność w Waszej branży?
Przemysł bardzo zmienił się ze względu na personalizację i indywidualne podejście do każdego klienta. Wiele osób oczekuje spersonalizowanych produktów, które wymagają od producentów dużej elastyczności. Wiele firm, które dotychczas produkowały kilka modeli produktów na dużą skalę odchodzą do lamusa, a pozostają tylko te, które są w stanie sprostać oczekiwaniom. Nie ma co ukrywać, że jest to bardzo trudne.
Zorganizowanie procesu, którego czas dostawy coraz częściej liczony jest już nawet nie w tygodniach, a w dniach, jest wymagające. Jeżeli zakład ma odnieść sukces potrzebujemy ludzi, którzy mają w sobie pasję do takich rozwiązań. Interesują się optymalizacją procesów itp.
Czy dobrze rozumiem, że właśnie takich pracowników udało się znaleźć w Lublinie?
Tak. W dużej mierze naszą kadrę tworzą absolwenci Lubelskich uczelni. Są to osoby dobrze wykształcone, posiadające niezbędną branżową wiedzę. Dziś nasz lubelski oddział tworzy około 40 osób. Jednak mamy nadzieję, że ta liczba będzie szybko rosła w 2021 roku.
Rynek pracy w Lublinie nie jest zbyt duży. Ma to oczywiście swoje wady i zalety. Na pewno można powiedzieć, że ludzie i firmy dobrze się znają. Poza tym wielu pracowników jest przywiązanych do swoich pracodawców, a to dodatkowe wyzwanie podczas budowania zespołu.
Ja, jako przedstawiciel spółki, jestem bardzo zadowolony z tego jaki udało mi się zbudować zespół. Jestem przekonany o naszym potencjale rozwojowym. Wiem, że Lublin będzie bardzo dużym wzmocnieniem dla marki Turck.
Dlaczego firma zdecydowała się ulokować swoją nową fabrykę w Lublinie?
Przyznam szczerze, że nie uczestniczyłem w procesie decyzyjnym. Wiem, że Zarząd rozważał bardzo różne lokalizacje w całej Europie. Między innymi na Litwie, Węgrzech czy w Rumunii. W Polsce wskazane zostały dwie potencjalne lokalizacje – Lublin i Rzeszów. Każde z miast otrzymywało punkty w różnych obszarach: ekonomicznych, technicznych czy logistycznych. W sumie było ich 100, a Lublin zgromadził aż 96. Warto zaznaczyć, że w przydzielaniu oceny mocno punktowane było wsparcie ze strony lokalnego samorządu.
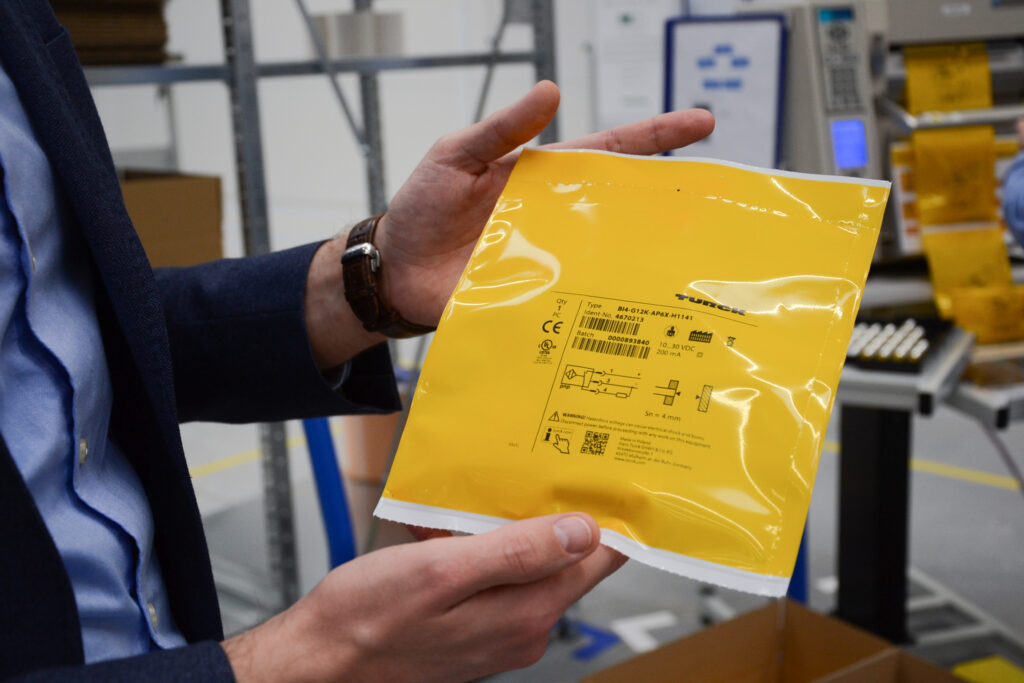
Wiem, że w związku z otwarciem nowego zakładu musiał Pan zdecydować o przeprowadzce na Lubelszczyznę ze Śląska. Zakładam, że nie była to łatwa decyzja.
Wydaje mi się, że takie decyzje nigdy nie są łatwe. Przeprowadzenie się wraz z całą rodziną z drugiej części Polski było wymagające. Mam tu na myśli absolutną zmianę otoczenia i znajomych. Przyznam, że do Lublina przyjechałem pierwszy raz w związku z tym projektem. Nigdy wcześniej nie zdarzyło mi się być tutaj.
Mimo to pamiętam, że miałem bardzo dobre wrażenia już przy pierwszej wizycie. Wspólnie z żoną uznaliśmy, że jest to dobre miejsce do życia. Jesteśmy pozytywnie nastawieni do tego miasta. Fantastyczna atmosfera, dobra komunikacja, klimat Starego Miasta i wszystkie wydarzenia kulturalne czy sportowe tworzą niesamowitą więź z tym miastem.
Wszystko czego można oczekiwać od życia w mieście tutaj jest. A jednocześnie jest ta bliskość regionu bardzo atrakcyjnego turystycznie. Można wyjechać, odpocząć. Myślę, że Lublin będzie przyciągał wielu ludzi i biznesów. Argument? Tu się po prostu dobrze mieszka.