Ostatnia dekada to czas dynamicznego rozwoju Specjalnej Strefy Ekonomicznej w Lublinie, w której swoje inwestycje lokowały czołowe globalne koncerny realizujące projekty wpisujące się w megatrend Przemysłu 4.0, którego istotnym elementem jest automatyzacja procesów produkcyjnych. Jednym z przedstawicieli tej grupy inwestorów jest niemiecki koncern Turck, którego dyrektorem zakładu w Lublinie jest Przemysław Brzeziewski.
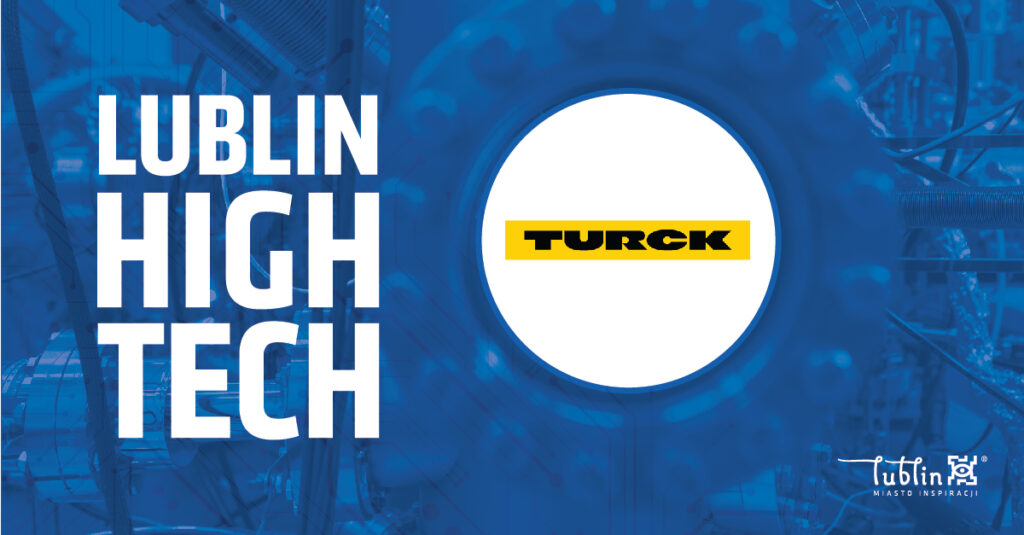
W czym specjalizuje się Państwa firma?
TURCK jest globalnym, zorientowanym na klienta partnerem w dziedzinie rozwiązań z zakresu automatyki przemysłowej. Prawie 60 lat temu rozpoczęliśmy naszą przygodę z automatyką od realizacji zamówienia na wzmacniacze separacyjne, potem przyszła kolej na różnego typu czujniki oraz produkcję komponentów Connectivity (wybrane typy czujników i przewody są wytwarzane również w zakładzie w Lublinie). Wraz z rozwojem techniki mikroprocesorowej w naszej ofercie pojawiły się moduły zdalnych wejść/wyjść – dzisiaj oferowane również z zaimplementowaną logiką, systemy identyfikacji RFID, moduły HMI oraz sterowniki. Oferujemy własne rozwiązania chmurowe z możliwością obróbki danych w czasie rzeczywistym oraz urządzenia brzegowe, dzięki którym można sterować maszynami bezpośrednio z chmury. Większość naszych systemów zaczyna się od różnego rodzaju czujników umieszczonych w różnych urządzenia. Te informacje, które spływają z procesów z różnych czujników historycznie były wykorzystywane w różnego typu sterownikach do wydawania prostych sygnałów w jaki sposób maszyna ma zareagować. Natomiast dzisiaj coraz więcej mamy rozwiązań, które są wysyłane do chmury, gdzie są poddawane bardziej zaawansowanym analizom, przy pomocy sztucznej inteligencji i obróbce typu Big Data. Dopiero na tej podstawie, są potem podejmowane określone działania i wyciągane wnioski. Można powiedzieć, że konsekwentnie podążamy drogą od dostawcy komponentów po wiodącą firmę zajmującą się cyfrową automatyzacją procesów.
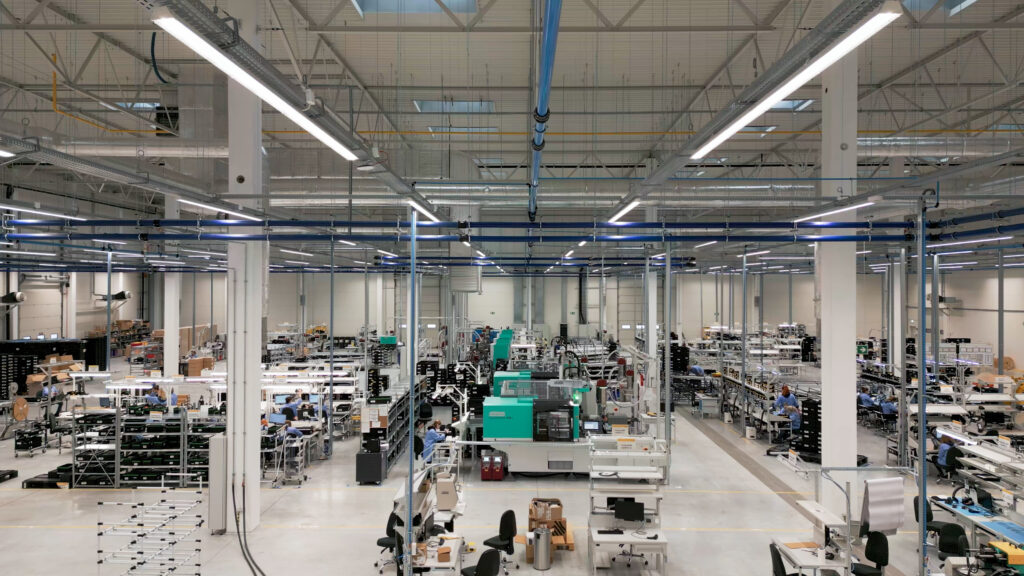
Ilu pracowników zatrudnia Państwa firma, kim są kluczowi członkowie Państwa zespołu?
Na dziś w naszej lokalizacji w Lublinie zatrudnionych jest 200 osób. Dużą część naszego zespołu stanowią pracownicy produkcji. Oprócz tego, nasz zespół składa się ze specjalistów zajmujących się realizacją projektów związanych z uruchomieniem produkcji kolejnych typów wyrobów. Tego typu projekty wymagają interdyscyplinarnych zespołów w obszarach inżynierii procesu, jakości, planowania, zakupów, ale również controllingu i finansów. Właściwie wszyscy nasi pracownicy pochodzą z Lublina i okolic, a także są absolwentami uczelni lubelskich. Jestem chyba tak naprawdę jedynym wyjątkiem – osobiście pochodzę ze Śląska.
Jaka część rozwiązań tworzona jest w Lublinie i co o tym zdecydowało?
Na tym etapie naszego rozwoju zajmujemy się głównie uruchamianiem produkcji istniejących wyrobów. Jednak nie są to klasyczne transfery linii produkcyjnych z innych lokalizacji. W dużej mierze nasze linie produkcyjne tworzymy od nowa, definiując technologie i kupując nowe wyposażenie. Oprócz tego, wspólnie z działem R&D w Niemczech rozpoczęliśmy właśnie projekt wdrożenia do produkcji nowej generacji innowacyjnych czujników, które mają trafić na rynek w 2025. Na tym etapie mamy szansę brać udział w opracowywaniu konstrukcji czujnika, a następnie w jego testach i walidacji. Uczestnictwo od początku w takim projekcie to świetne doświadczenie dla naszego zespołu. W dalszym etapie planujemy otworzenie pierwszego w grupie Turck działu R&D i IT w Polsce.
Jakie są przewagi państwa rozwiązań w porównaniu do podobnych technologii dostępnych na rynku?
Rozwój firmy Turck charakteryzuje się innowacjami. Dzięki swoim pomysłom i rozwiązaniom zawsze byliśmy jednym z pionierów i stymulatorów rozwoju automatyki przemysłowej. Daliśmy światu pierwsze czujniki indukcyjne z współczynnikiem korekcji 1 dla wszystkich metali. To firma Turck w roku 1988 stworzyła na potrzeby fabryki Forda w Europie pierwszy system fieldbus, który nazwano Sensorplex, w roku 2006 wprowadziliśmy system RFID w IP67 z możliwością wymiany danych w locie bez potrzeby zatrzymywania linii produkcyjnej, w roku 2016 pierwsi zaimplementowaliśmy logikę do zwykłych modułów I/O i nazwaliśmy ją ARGEE; od 2018 roku w duchu Przemysłu 4.0 oferujemy naszym klientom rozwiązania chmurowe Turck Cloud Services. Na podstawie naszych wieloletnich doświadczeń w produkcji układów elektroniki jako bazy do elementów automatyki, zaczęliśmy oferować rozwiązania pod konkretne potrzeby i to w większości nie związane stricte z automatyką przemysłową. Wspomnę chociażby o elektronice sterującej pompą wodną w samochodach osobowych, które produkujemy na potrzeby dwóch dużych niemieckich koncernów. W kolejnym kroku powstała firma Turck Mechatec, która zajęła się prefabrykacją szaf, a kilka lat temu przejęliśmy firmę Vilant System. Ta fińska firma może pochwalić się ponad 1000 kompleksowych wdrożeń systemów RFID do wsparcia procesów w szeroko pojętej logistyce i zarządzaniu majątkiem trwałym. Turck Vilant System oferuje dobór odpowiedniego sprzętu, stworzenie bazy danych i pomoc w jej integracji z wykorzystywanym przez inwestora systemem ERP czy MES do zarzadzania produkcją lub całym zakładem. Firma świadczy też wsparcie w cyklu 7/24. Jako Turck Polska od kilku lat z powodzeniem oferujemy klientom kompletne systemy przywoławcze, systemy kontroli pobrań czy wreszcie szeroko pojęty Condition Monitoring tak ważnych parametrów jak wibracje, temperatura, wilgotność, poziom czy wskaźniki OEE. Kontrola tych parametrów jest kluczowa przy wdrażaniu predykcyjnego utrzymania ruchu oraz wpływa na zwiększenie efektywności pracy maszyn i wykorzystania zasobów ludzkich.
Kto jest głównym odbiorcą waszych rozwiązań?
Patrząc na sam zakład w Lublinie, który jest 7-mym z kolei i jednocześnie najnowszym zakładem produkcyjnym w Turck-Group, cała produkcja jest wysyłana do centrum dystrybucji w Niemczech i stamtąd wysyłana do obiorców z poszczególnych krajów. Nasza grupa docelowa to producenci maszyn oraz linii przemysłowych w wielu branżach, z których jako wiodące można wymienić branże: motoryzacyjną, intralogistyki, chemiczną, spożywczą czy maszyn mobilnych. W Lublinie, zajmujemy się wyłącznie produkcją. Dział odpowiadający za sprzedaż to osobna spółka w Turck-Group z siedzibą w Opolu. W sumie jesteśmy w grupie kilku krajów, które w naszej organizacji posiadają więcej niż jeden podmiot – w naszym przypadku jest to Turck Automation Technology w Lublinie i Turck Sp. z o.o. w Opolu.
Nasze rozwiązanie stosowane jest w wielu wiodących firmach technologicznych na świecie. Oczywiście, aby użyć nazwy konkretnej firmy trzeba mieć na to odpowiednie zgody. Z ciekawszych ostatnich sukcesów mogę wspomnieć o stanowiskach testowych wykonanych z wykorzystaniem naszej technologii RFID przez Turck Vilant dla jednego z wiodących niemieckich producentów samochodów klasy premium o wartości 3,5 mln Euro. Kolejny trwający jeszcze projekt, to całkiem nowa linia do produkcji samochodów amerykańskiej marki, w zakładzie ulokowanym w Belgii. Cały projekt oparty jest na naszych modułach I/O, naszym systemie RFID i okablowaniu – wartość dla nas to około 1,5 mln Euro. Z naszego rynku pewnie musielibyście zapytać moich kolegów z Opola. Wiem, że w zeszłym roku oferowali, i to z sukcesem, naszej największej grupie petrochemicznej specjalne moduły do kontroli warunków w szafach zasilających. Kilkaset modułów już znalazło zastosowanie, a sprawa jest nadal rozwojowa.
Jakie widzi Pan możliwości współpracy w szerszym zakresie z lokalnymi uczelniami i firmami z rynku lubelskiego?
Szef naszego działu technicznego jest absolwentem Wydziału Mechanicznego na Politechnice Lubelskiej.
Widzimy kilka obszarów, które możemy wspólnie z Politechniką rozwijać, np., czynna partycypacja w uruchomieniach nowych kierunków II stopnia, zorientowanych strikte na potrzeby firm produkcyjnych naszego sektora pod kątem szeroko rozumianego inżynieringu czy utrzymania ruchu. W naszych rozważaniach pojawił się także pomysł organizacji studiów dualnych. Upatrujemy w tym dużą wartość dodaną zarówno dla nas jako organizacji, jak i dla uaatrakcyjnienia oferty dydaktycznej uczelni. Jesteśmy również otwarci na to, żeby studenci piszący prace dyplomowe, realizowali projekty przy wykorzystaniu naszych maszyn i procesów z nimi związanych.
Przy tym wszystkim, nie możemy zapominać, że zakład produkcyjny to nie tylko produkcja. Nasza codzienność to realizacja wielu funkcji związanych z planowaniem zakupów, logistyką, księgowością czy kontrolingiem. To z kolei otwiera możliwość współpracy z wydziałami ekonomicznymi, nie tylko Politechniki Lubelskiej. Jeżeli chodzi o lokalne firmy, to mamy partnerów z samego Lublina, którzy wspierają nas w tworzeniu linii produkcyjnych oraz wykonują dla nas elementy wyposażenia. W miarę możliwości poszukujemy firm, które mogłyby produkować i dostarczać komponenty, które będą wykorzystane do naszej produkcji.
Jakie działania może miasto Lublin wraz z partnerami instytucjonalnymi podjąć, aby rozwijać swój potencjał jako centrum tworzenia wysokich technologii?
Ważnym elementem jest na pewno dostępność terenów inwestycyjnych. Rozwojowi miasta jako centrum wysokich technologii sprzyjałaby niewątpliwie również regularna organizacja targów przemysłowych i wystaw w obszarze Przemysłu 4.0.
Bardzo dziękujemy za rozmowę.