W świecie, w którym innowacje napędzają przyszłość motoryzacji, to właśnie młodzi ludzie coraz częściej stają się autorami przełomowych rozwiązań. Lublin od lat kojarzony jest z silnym zapleczem akademickim, ale coraz wyraźniej staje się również miejscem, gdzie młodzi ludzie rozwijają innowacyjne projekty i zdobywają realne doświadczenie technologiczne. To miasto, w którym edukacja spotyka się z praktyką, a pasja – z możliwościami. Zapraszamy do lektury wywiadu z uczniami Zespołu Szkół Transportowo-Komunikacyjnych w Lublinie – Adamem Motylem, Filipem Grabowiczem, Jakubem Wolskim. Przy wsparciu swojego opiekuna – Konrada Pietraszka – opracowali edu-makietę zacisku elektrycznego hamulca ręcznego (EPB) dla firmy Borg Automotive Sp. z o.o.
W rozmowie opowiadają o pracy zespołowej, wsparciu lokalnych firm, potencjale edukacyjnym Lublina i swoich planach na przyszłość. To głos młodych, którzy nie czekają na „jutro” – tylko już dziś budują je własnymi rękami.

Zacznijmy od samego projektu – jak narodził się pomysł stworzenia makiety zacisku hamulca elektrycznego? Czy inspirowaliście się jakimś konkretnym zastosowaniem przemysłowym?
Pomysł narodził się podczas jednej z rozmów o nowoczesnych rozwiązaniach w motoryzacji. Zaciski hamulców elektrycznych (EPB) stają się coraz bardziej powszechne, a jednocześnie pozostają dość „tajemnicze” – ich działanie jest ukryte wewnątrz pojazdu i trudne do zademonstrowania bez specjalistycznego sprzętu. Zainspirowało nas to do stworzenia makiety, która umożliwi zrozumienie zasady ich działania – zarówno od strony mechanicznej, jak
i elektronicznej. Wzorowaliśmy się częściowo na rzeczywistych zastosowaniach w przemyśle motoryzacyjnym, zwłaszcza w firmach takich jak BORG Automotive.
Jak wyglądała praca nad systemem sterowania? Czy zastosowanie Arduino i programowalnych trybów pracy było wyzwaniem?
Tak, to był jeden z trudniejszych etapów. Musieliśmy dobrać odpowiedni mikrokontroler, napisać oprogramowanie i przetestować różne tryby pracy zacisku. Arduino pozwoliło nam na elastyczne podejście – mogliśmy zaprogramować m.in. tryb diagnostyczny. Dużym wyzwaniem było zsynchronizowanie działania elektroniki z mechaniką zacisku. Aby sobie z nim poradzić, konieczne było podjęcie wielu prób i kolejnych wizyt w firmie. Polegało to między innymi na dobraniu odpowiedniego czasu pracy silnika, który znajduje się w zacisku.
Co sprawia, że Wasz projekt jest innowacyjny? Jak udało się „ożywić” zacisk, który w normalnych warunkach działa tylko po zamontowaniu w samochodzie?
Innowacyjność naszego projektu polega na tym, że stworzyliśmy w pełni funkcjonalną makietę zacisku EPB działającą poza samochodem. Dzięki zastosowaniu Arduino i własnemu układowi sterowania, udało się nam odwzorować działanie zacisku tak, jakby był zamontowany w aucie. Co więcej, makieta ma przekrój oraz rozłożone komponenty, co umożliwia pragmatyczne podejście do nauki o tym mechanizmie. Gdy firma rekrutuje nowych pracowników, będzie jej potrzebne zapoznanie ich z budową i działaniem zacisku EPB. W tym celu bardzo dobrze sprawdzi się nasza makieta. Oprócz tego, na makiecie pokazany jest taki sam zacisk w rozbiciu na części, co może pomóc również bardziej doświadczonym pracownikom przy problemach konstrukcyjnych.
Makieta zawiera nie tylko działający zacisk, ale też jego przekrój i rozłożone komponenty. Jak wpadliście na pomysł takiej formy edukacyjnej i demonstracyjnej?
Zależało nam na tym, żeby makieta nie była tylko pokazem technologii, ale też narzędziem edukacyjnym. Chcieliśmy, aby każdy – nawet osoba niezwiązana z motoryzacją – mógł zrozumieć, jak działa taki hamulec. Pomysł z przekrojem i rozłożeniem części zrodził się naturalnie – to najlepszy sposób na pokazanie zasady działania od środka.
Jak zbudowaliście zespół? Czy wcześniej współpracowaliście przy innych projektach, czy ten konkurs Was połączył?
Znamy się z technikum i już wcześniej mieliśmy okazję razem działać – czy to przy projektach szkolnych, czy prywatnych pomysłach. Ten konkurs był jednak naszym pierwszym dużym, wspólnym wyzwaniem i świetnie pokazał, że potrafimy skutecznie współpracować jako zespół. Adam zajął się pisaniem programu do mikrokontrolera Arduino oraz projektem okablowania, zaś Jakub i Filip zajęli się projektowaniem układu części na makiecie oraz modelowaniem 3D panelu sterującego.
Co było dla Was najtrudniejsze – od strony technicznej lub organizacyjnej, ale też w kontekście pracy zespołowej? Czy były momenty, kiedy pojawiły się kryzysy?
Najtrudniejsze było połączenie nauki, życia prywatnego i intensywnej pracy nad projektem. Bywały momenty stresu, szczególnie gdy coś nie działało lub terminy goniły. Dzięki dobrej komunikacji i podziałowi zadań potrafiliśmy się wspierać i razem szukać rozwiązań. Z perspektywy czasu te trudności tylko nas wzmocniły.
Podczas pracy nad projektem współpracowaliście z firmą BORG Automotive – jak wyglądały spotkania, wizyty i konsultacje? Czego konkretnie nauczyliście się od specjalistów firmy?
Spotkania z ekspertami z BORG Automotive były bardzo cenne. Mieliśmy okazję zobaczyć, jak wygląda profesjonalna regeneracja i testowanie zacisków. Pracownicy dzielili się z nami praktyczną wiedzą, której nie znajdzie się w podręcznikach – np. jak diagnozuje się uszkodzenia czy jak wygląda proces regeneracji. Ich wskazówki pomogły nam ulepszyć projekt i uniknąć wielu błędów.
Jak duży wpływ miała współpraca z BORG Automotive na jakość i kierunek projektu? Czy coś zmieniło się w Waszym podejściu dzięki tym rozmowom?
Bez tej współpracy projekt z pewnością nie byłby na tak wysokim poziomie. Dzięki konsultacjom mogliśmy dobrać odpowiednie komponenty, lepiej zrozumieć mechanikę zacisku i poprawić niektóre rozwiązania. Zaczęliśmy też patrzeć na naszą makietę bardziej profesjonalnie – nie tylko jako szkolny projekt, ale jako coś, co może mieć realne zastosowanie. Gdy przenieśliśmy się z naszą makietą do firmy, wyszły drobne błędy w programie sterującym i podpisach części. Mogliśmy jednak liczyć na wyrozumiałość i pomoc pracowników zakładu Borg Automotive, którzy pomogli nam w ich usunięciu.
Jak wyglądały kolejne etapy realizacji makiety – od pomysłu, przez projektowanie i zamawianie części, aż po programowanie i montaż?
Najpierw stworzyliśmy koncepcję i szkic działania. Potem przeszliśmy do zbierania części – część zdobyliśmy dzięki współpracy z BORG, inne zamawialiśmy lub tworzyliśmy sami. Największą częścią, którą wykonaliśmy sami była obudowa panelu sterującego. Jego zaprojektowanie leżało po naszej stronie, zaś wydruk wykonany został w firmie. Kolejnym krokiem było zaprojektowanie systemu sterowania, programowanie Arduino i testowanie działania zacisku. Na koniec skupiliśmy się na estetyce i finalnym montażu całości na estetycznej podstawie. Nad naszą makietą pracowaliśmy zarówno w domu, w firmie, jak i podczas zajęć szkolnych.
Zadbaliście również o estetykę makiety, co rzadko spotyka się w pracach technicznych na poziomie uczniowskim. Dlaczego zależało Wam na wizualnej stronie projektu?
Uważamy, że forma ma znaczenie – szczególnie jeśli chce się dotrzeć do szerszego grona odbiorców. Estetyczna prezentacja przyciąga uwagę i ułatwia zrozumienie działania makiety. Chcieliśmy też pokazać, że projekt techniczny może być jednocześnie funkcjonalny i atrakcyjny wizualnie.
Gratulacje – zdobyliście I miejsce w konkursie „Młodzi Innowatorzy” i zaprezentowaliście swój projekt podczas Innovation Open Day na Politechnice Lubelskiej! Co dla Was znaczy ten sukces?
To było niesamowite uczucie. Praca nad projektem trwała wiele tygodni, więc samo znalezienie się w finale było dla nas dużym wyróżnieniem. Gdy ogłoszono, że zdobyliśmy I miejsce, pojawiła się euforia, niedowierzanie i ogromna satysfakcja. Ten sukces to nie tylko nagroda za naszą pracę, ale też motywacja, by dalej działać i rozwijać się w kierunku inżynierii.
Prezentowaliście swój projekt na Innovation Open Day na Politechnice Lubelskiej. Jak oceniacie to doświadczenie – kontakt z naukowcami, pytania, opinie?
To było bardzo inspirujące. Mieliśmy okazję porozmawiać z naukowcami, inżynierami i studentami, którzy zadawali konkretne, techniczne pytania i dawali ciekawe sugestie. To doświadczenie pokazało nam, że nasz projekt ma potencjał i jest dobrze odbierany także przez osoby z dużym doświadczeniem. Jeśli chodzi o nasz temat pracy, jako jedyni podjęliśmy się jego wykonania. Natomiast naszą konkurencję stanowiły rozwiązania innych problemów zgłoszonych przez firmy. Trochę stresowaliśmy się przed jego zaprezentowaniem, jednak mamy już w tym względzie pewne doświadczenie, ponieważ rok wcześniej uczestniczyliśmy już we wcześniejszej edycji tego konkursu, zajmując drugie miejsce.
Lublin to miasto z rosnącym potencjałem technologicznym – czy widzicie tu dla siebie przyszłość zawodową?
Zdecydowanie dostrzegamy potencjał Lublina. Myślimy o studiach technicznych właśnie tutaj, a może i o własnym startupie w przyszłości. Lublin ma świetną infrastrukturę, uczelnie i coraz więcej firm z branży automatyki czy motoryzacji – to dobre miejsce na rozwój. Na ten moment myślimy przede wszystkim o ukończeniu technikum, zdaniu matury oraz egzaminów zawodowych. Kolejnym krokiem będzie dostanie się na studia – wtedy możliwe będzie funkcjonowanie w odpowiednim środowisku do rozwijania horyzontów i możliwe, że wtedy zajmiemy się własnym startupem biznesowym.
Jakie inne projekty technologiczne chcielibyście jeszcze zrealizować jako zespół? Czy są już kolejne pomysły na horyzoncie?
Mamy już kilka pomysłów ale zostawimy je dla siebie , jak to mówią profesjonaliści „tajemnica zawodowa„ ale jesteśmy pewni, że jeszcze nie raz o nas usłyszycie be jest to nasza pasja i chcemy ją rozwijać 🙂
Na koniec – co powiedzielibyście innym uczniom, którzy chcą zrobić coś ciekawego, ale nie wiedzą, od czego zacząć?
Po prostu zacznijcie – nawet od małych rzeczy. Nie bójcie się pytać, szukać wsparcia i popełniać błędów. Warto działać w zespole, bo wspólna praca to nie tylko szybsze postępy, ale też lepsza motywacja. A przede wszystkim – nie czekajcie na „idealny moment”. On jest teraz!
Dziękujemy za rozmowę i trzymamy kciuki za Wasz dalszy rozwój!
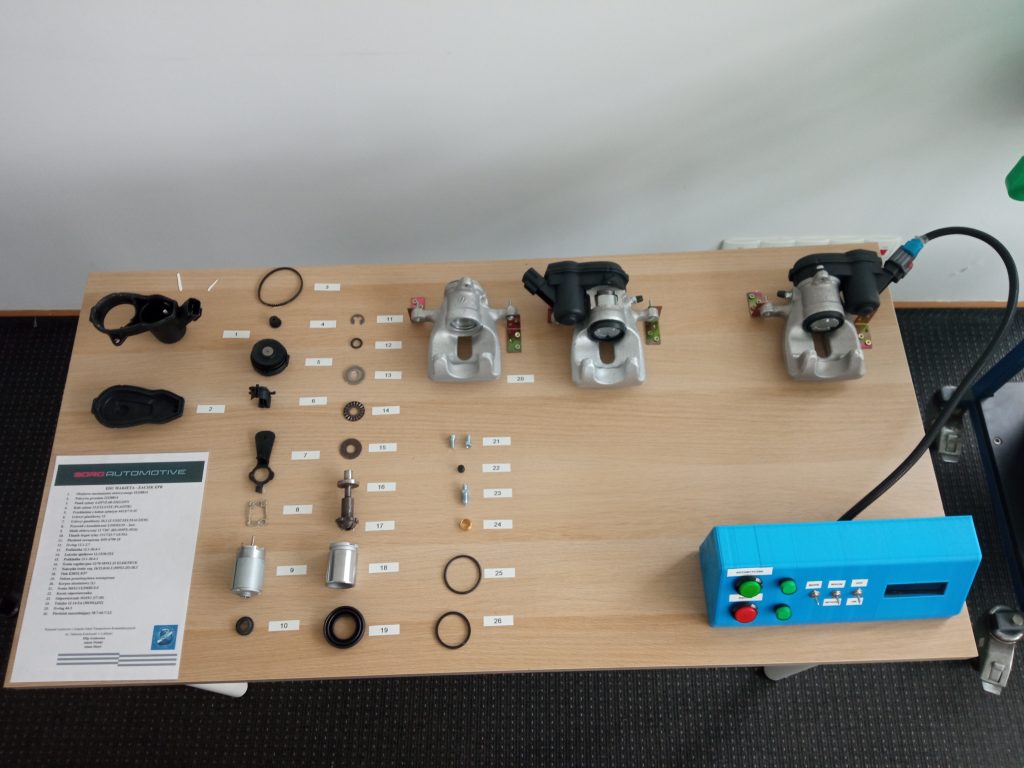
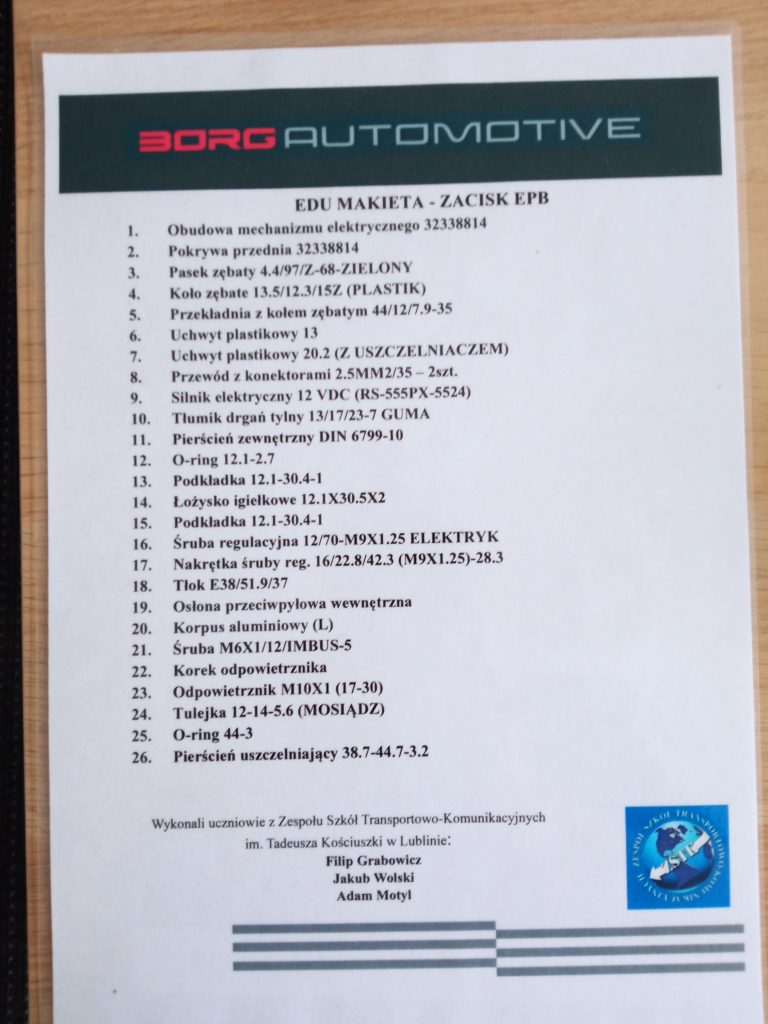
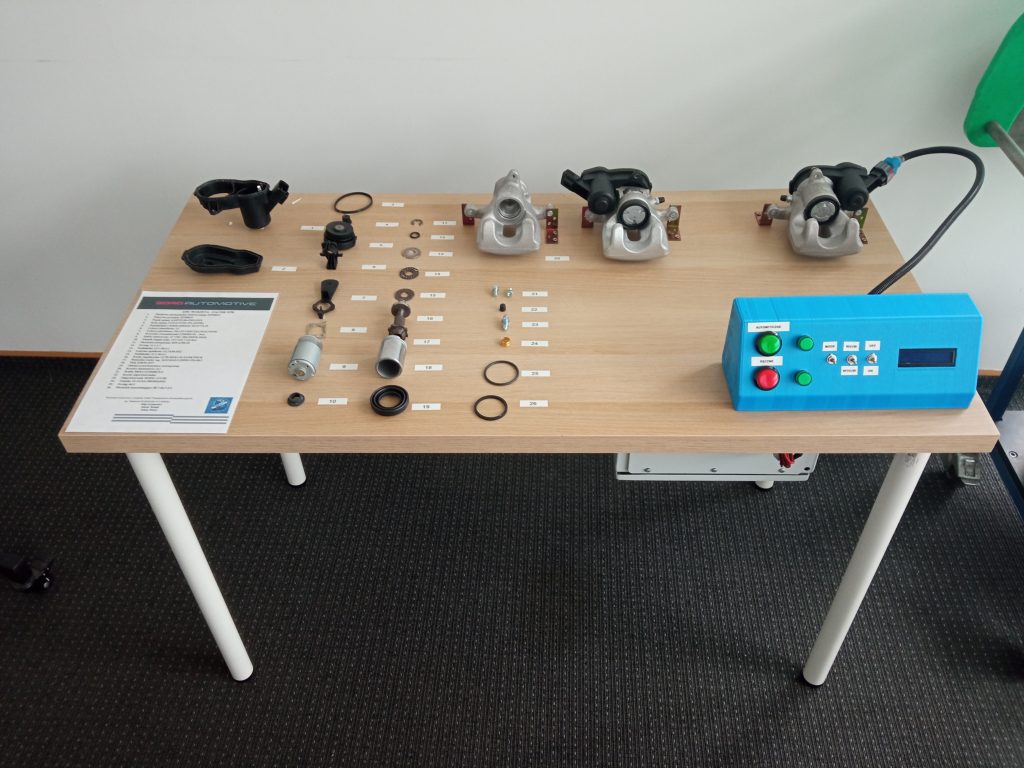